The Client
Flatworld Solutions was contacted by a company that develops innovative, custom engineered aluminum and fiberglass overhead utility and communications solutions products for communications companies, electric companies, and other clients.
The client contacted Flatworld Solutions looking for a partner that could help them re-design and manufacture one of their products. They also needed a partner that could engineer the design at a low budget, without sacrificing on accuracy and one that could complete it within 45 days.
Our ability to respond, history with this type of engineering, and affordability convinced the client to select the Flatworld Solutions team.
The Problems
The Flatworld Solutions team encountered many challenges with the project. Some of these challenges included -
- Missing Specifications - The aluminum cast product that was to be re-designed was missing its specifications, which were necessary to create both 3D drawings and 3D modeling.
- Missing Grooves - The internal grooves of the product were unavailable. This would lead to challenges in scanning the product for analysis.
- Limited Timeframe - Because the specifications and grooves were missing, the ability to meet the 45 day deadline would be put to the test.
The Solutions
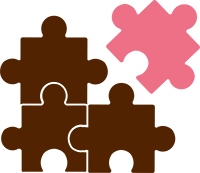
Modeling can be a difficult and time consuming task that requires only the most highly trained experts, so we began the project by first performing a paid trial project and sending it back to the client for review. The client was satisfied with the trial project and requested that Flatworld Solutions continue.
Flatworld Solutions assigned 2 resources to the project, both experts in the field. The client then sent 3 physical samples to the Flatworld Solutions team, along with the measurements and specifications of the products. The Flatworld team then used a 3D scanner to scan the products, and collected the point cloud data.
Using SolidWorks, the team then completed surface modeling for the product. Throughout the process, the QA team consistently monitored for quality and accuracy, and approved the final designs.
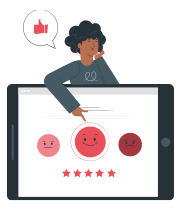
The Results
Flatworld Solutions was successfully able to complete the project within the 45-day timeframe, with a reported accuracy level of over 90%. The solution was well received by the client, as they were pleased at both the quality of the final deliverable, and the cost with which we were able to complete it. The client was so satisfied that they recommended Flatworld Solutions to their business partners.
For more information about our mechanical engineering services, or any of our engineering and design services, contact Flatworld Solutions today.
Contact UsAvail best-in-class services at affordable rates
Our Customers



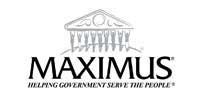

Key Differentiators
Case Studies
-
Flatworld Solutions provided customized CNC programming using MasterCAM
-
Flatworld Provided CFD Simulation Services to a Leading HVAC Products Manufacturer
-
Flatworld Solutions Offered Mechanical Instrument Drafting and Detailing Services to an Engineering Consultant
-
Flatworld Solutions Offered US Client with 2D to 3D Mechanical Legacy Drawing Conversion
-
Flatworld Solutions Provided Reverse Engineering of Machine Parts to a Client
Join the growth phase at Flatworld Solutions as a Partner
Service distributorship and Marketing partner roles are available in select countries. If you have a local sales team or are a person of influence in key areas of outsourcing, it's time to engage fruitfully to ensure long term financial benefits. Currently business partnerships are open for Photo Editing, Graphic Design, Desktop Publishing, 2D and 3D Animation, Video Editing, CAD Engineering Design and Virtual Walkthroughs.
Reach out to us for a quick direct response from decision makers at the Flatworld Solutions global team.

USA
Flatworld Solutions
116 Village Blvd, Suite 200, Princeton, NJ 08540
PHILIPPINES
Aeon Towers, J.P. Laurel Avenue, Bajada, Davao 8000
KSS Building, Buhangin Road Cor Olive Street, Davao City 8000
INDIA
Survey No.11, 3rd Floor, Indraprastha, Gubbi Cross, 81,
Hennur Bagalur Main Rd, Kuvempu Layout, Kothanur, Bengaluru, Karnataka 560077