Point cloud data has been around for a while and has found application in many areas. Point cloud data is generated using LiDAR wherein laser beams bounce off objects and are captured as point data, along with attributes such as RGB information. Point cloud data has enabled the creation of detailed digital models like building information models (BIMs), which are digital representations of buildings to be built. These digital representations of real-world objects help stakeholders to monitor assets and their use and changes.
In recent times, point cloud technology has been used to convert a physical factory into a digital model using point cloud conversion. 3D scanning services can be leveraged to obtain detailed point cloud data of real-world assets and these can be scaled up to represent large-scale and complex entities like factories. Technology is now sufficiently advanced that point cloud lets anyone run a factory from anywhere. This article presents information on digital twin simulation and smart factory automation and explains how you can convert a physical into a digital factory using point cloud modeling and point cloud technology simulation.
What is a Digital Twin of a Factory?
A digital twin is a relatively new term that refers to an exact digital replica of real-world assets, such as a factory. These digital twins are created using 3D point cloud data of a facility or asset and contain pertinent and detailed information of the asset or facility. The digital twin also gets updated with real-time information of the physical asset through IoT sensors attached to the physical asset. This allows for real-time monitoring of the physical asset, which can result in digital twin-driven smart manufacturing.
How is a Digital Twin or Model of a Factory Created?
The digital twin in the smart factory is created using point cloud technology. Bridging the physical into the digital factory is a complex process and that's why, if you're looking to create a digital twin simulation, you might want to hire the services of specialized providers who will capture the data of the asset using LiDAR technology. Once the point cloud technology is obtained, it needs to be digitized and developed into a digital twin to enable things like factory remodeling or smart factory automation. A digital twin will also be needed to be provided with “live” data from sensors fitted onto the physical assets/objects.
What are the Benefits of a Digital Model of a Physical Factory?
When you use point cloud data to create a digital twin or digital model of a physical factory, you can leverage many benefits, including -
-
Enhanced Availability and Reliability
With a digital twin, you can more effectively monitor, simulate, and control various assets, processes, or networks in the factory to improve performance and efficiency. The more information that is in your digital model, the better it is, and we are seeing increasingly more sophisticated digital twins that are helping companies better manage the operations in their factories.
-
Reduced Risk
When you convert your factory into a digital model, you can reduce process- and asset-related issues and prevent unplanned downtime. With this, the health and safety of your employees and work environment can be protected. You can also proactively identify risk-related issues and take steps to mitigate them so that they do not become a major hindrance further down the line.
-
Low Maintenance Costs
With a digital twin, you also get information on all your assets and processes at your fingertips, allowing you to identify and fix any issues well before they become major problems. You can predict problems before things like breakdowns occur and proactively order relevant parts and equipment and schedule repairs at times when there is the least disruption to business processes.
-
Improved Production
With data coming in from physical assets in the factory to the digital model, you get insights into the performance of your processes and assets in real-time. With this, you can ensure product quality and minimize any impacts on your supply chain. A digital twin of experimental smart manufacturing also provides you with real-time capabilities and analytics to help you ramp up production and identify opportunities for savings and efficiency.
Outsource Point Cloud and Digital Modeling Services to Flatworld Solutions and Reap a Host of Benefits
Flatworld Solutions is a leading provider of a range of engineering services as well as comprehensive and detailed point cloud and digital modeling services. We can help manufacturing and consulting companies convert physical factory setups to digital models through point cloud data for various purposes. We cater to various applications like asset management, facility management/automation, factory remodeling, digital twin, etc. We also leverage multiple CAD software like CATIA, Revit, SolidWorks, etc., to provide our clients with cutting-edge services. Some tasks we can perform include -
- Convert paper to CAD model
- Convert point cloud scan data to a CAD model
- Create Revit families or CAD libraries for AR/VR training
- Create assets (MEP, firefighting, etc.) in digital/CAD models for asset tagging/facility management purposes (IoT framework application)
If you are looking for highly secure and professional point cloud and digital modeling services, contact us now to take a productive route to success.
Contact UsAvail best-in-class services at affordable rates
Our Customers



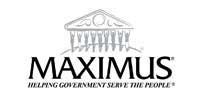

Key Differentiators
Case Studies
-
Flatworld Solutions provided customized CNC programming using MasterCAM
-
Flatworld Provided CFD Simulation Services to a Leading HVAC Products Manufacturer
-
Flatworld Solutions Offered Mechanical Instrument Drafting and Detailing Services to an Engineering Consultant
-
Flatworld Solutions Offered US Client with 2D to 3D Mechanical Legacy Drawing Conversion
-
Flatworld Solutions Provided Reverse Engineering of Machine Parts to a Client
Join the growth phase at Flatworld Solutions as a Partner
Service distributorship and Marketing partner roles are available in select countries. If you have a local sales team or are a person of influence in key areas of outsourcing, it's time to engage fruitfully to ensure long term financial benefits. Currently business partnerships are open for Photo Editing, Graphic Design, Desktop Publishing, 2D and 3D Animation, Video Editing, CAD Engineering Design and Virtual Walkthroughs.
Reach out to us for a quick direct response from decision makers at the Flatworld Solutions global team.

USA
Flatworld Solutions
116 Village Blvd, Suite 200, Princeton, NJ 08540
PHILIPPINES
Aeon Towers, J.P. Laurel Avenue, Bajada, Davao 8000
KSS Building, Buhangin Road Cor Olive Street, Davao City 8000
INDIA
Survey No.11, 3rd Floor, Indraprastha, Gubbi Cross, 81,
Hennur Bagalur Main Rd, Kuvempu Layout, Kothanur, Bengaluru, Karnataka 560077