The Client
Flatworld Solutions was contacted by a unique company that creates products which collect, store, and distribute clean water to an entire country. The client produced several products, including a water catchment device, inspect and pest control technology, leaf and debris removal systems, and more. These products were used for both "rain harvesting" (collecting rainwater for residential use) and home protection.
One of the products created by the client needed to be resized. They needed the new product to be larger than the existing product. Given the challenges associated with resizing plastic products, the client also wanted to hire a company that had engineers on staff with plastic component engineering experience.
The client selected Flatworld Solutions because of our swift response to their request, and our ability to produce resources that could work on their task as requested.
The Challenges
The client sent over several PPTs, 2D drawings, and 3D models to our team at Flatworld Solutions. They needed the product created in a software known as SolidWorks, which Flatworld Solutions had available.
Resizing plastic components is very different from other forms of resizing, such as with metal, which tend to scale more easily. This meant that we had to use the select resources with plastic component engineering experience to work on the tasks, of which fewer staff members were available. We also would need to complete the project in roughly 3 weeks, which would be challenging with so few resources to provide support.
The Solution
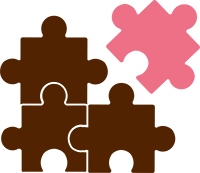
Our team had 4 resources on staff with experience in plastic component engineering, and all four resources were assigned to the task. Samples were initially created to ensure accuracy. Once approved, the team at Flatworld Solutions downloaded the files (which were sent via DropBox) and began resizing the components in SolidWorks as instructed.
Throughout the project, the Quality Assurance Team here at Flatworld Solutions reviewed each component and performed quality checks along the way for accuracy. The SolidWorks files were then sent back to the client upon completion of the project.
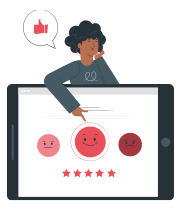
The Results
The team was able to deliver the product within the 3 week timeframe, and achieve an accuracy level of greater than 90%. The client was highly satisfied with the work, and immediately assigned two more projects to Flatworld Solutions, establishing a long term business partnership with our team.
For more information about our engineering solutions, including Mechanical, Structural, and Architectural solutions, contact Flatworld Solutions today.
Contact UsAvail best-in-class services at affordable rates
Our Customers



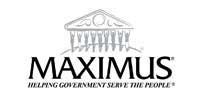

Key Differentiators
Case Studies
-
Flatworld Solutions provided customized CNC programming using MasterCAM
-
Flatworld Provided CFD Simulation Services to a Leading HVAC Products Manufacturer
-
Flatworld Solutions Offered Mechanical Instrument Drafting and Detailing Services to an Engineering Consultant
-
Flatworld Solutions Offered US Client with 2D to 3D Mechanical Legacy Drawing Conversion
-
Flatworld Solutions Provided Reverse Engineering of Machine Parts to a Client
Join the growth phase at Flatworld Solutions as a Partner
Service distributorship and Marketing partner roles are available in select countries. If you have a local sales team or are a person of influence in key areas of outsourcing, it's time to engage fruitfully to ensure long term financial benefits. Currently business partnerships are open for Photo Editing, Graphic Design, Desktop Publishing, 2D and 3D Animation, Video Editing, CAD Engineering Design and Virtual Walkthroughs.
Reach out to us for a quick direct response from decision makers at the Flatworld Solutions global team.

USA
Flatworld Solutions
116 Village Blvd, Suite 200, Princeton, NJ 08540
PHILIPPINES
Aeon Towers, J.P. Laurel Avenue, Bajada, Davao 8000
KSS Building, Buhangin Road Cor Olive Street, Davao City 8000
INDIA
Survey No.11, 3rd Floor, Indraprastha, Gubbi Cross, 81,
Hennur Bagalur Main Rd, Kuvempu Layout, Kothanur, Bengaluru, Karnataka 560077